At Right Brain Left Brain LLC, we specialize in Operational Excellence (OpEx) and Lean Six Sigma (LSS) transformations to help organizations optimize processes, improve efficiency, and reduce waste. With years of hands-on experience, we apply proven methodologies to ensure your business operates at peak performance while maintaining regulatory compliance. From process mapping to full-scale Lean transformations, we deliver sustainable improvements that drive real results.
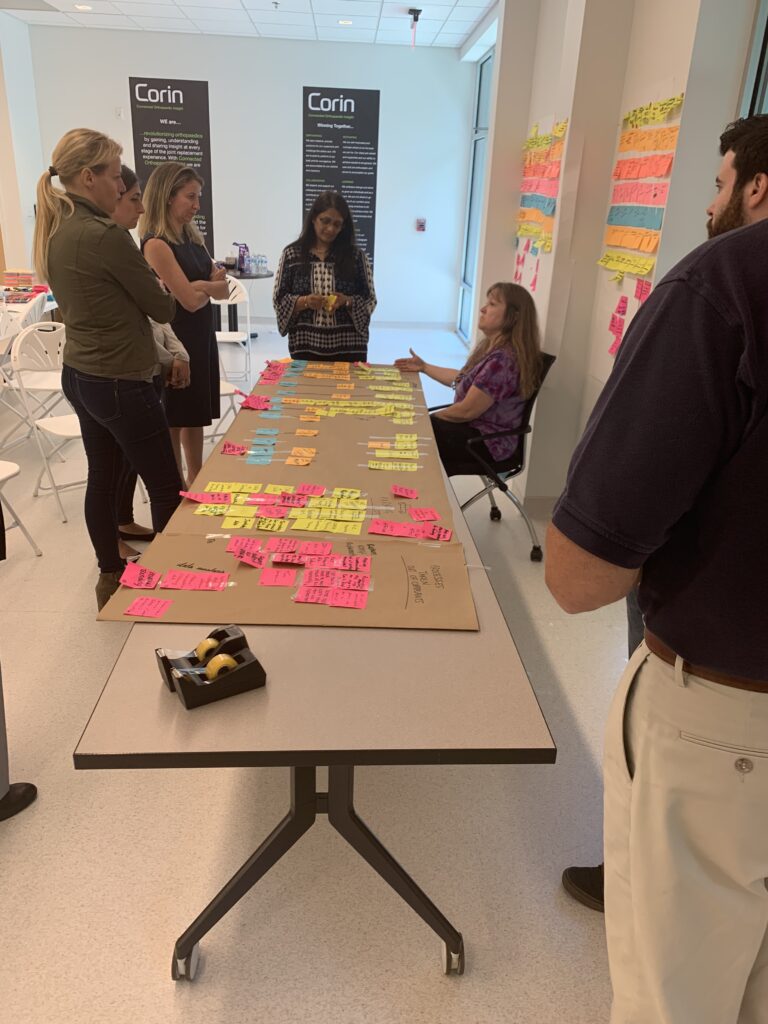
Our Operational Excellence (OpEx) and Lean Six Sigma (LSS) transformation services are designed to help businesses achieve greater efficiency, reduce costs, and improve overall performance. Whether you’re looking to streamline your production processes, improve quality, or enhance your company’s overall operational effectiveness, our team has the expertise to lead you through the journey to operational excellence.
Why Choose Right Brain Left Brain LLC?
At Right Brain Left Brain LLC, we take a hands-on approach to Operational Excellence and Lean Six Sigmatransformations. Our goal is not only to help you streamline your operations and improve efficiency but also to create a culture of continuous improvement within your organization. By integrating Lean principles with AI-enhanced tools and practical, results-driven strategies, we help you achieve long-term success and operational excellence.
1. Initial Assessment & Process Mapping:
Every successful Lean transformation begins with a thorough understanding of your current processes. We start by conducting a detailed assessment of your operations:
Data-Driven Analysis: We use data-driven insights to assess how resources are being utilized and pinpoint areas that require improvement.
Process Mapping: Our team works with yours to create detailed process maps that visualize the current state of your operations, from raw material inputs to final product delivery.
Bottleneck Identification: We identify bottlenecks, inefficiencies, and wasteful steps that are slowing down production or increasing costs.
2. Lean Six Sigma Methodologies:
We apply Lean Six Sigma methodologies to eliminate inefficiencies, reduce variability, and drive continuous improvement across your organization:
Value Stream Mapping: Using value stream mapping, we visualize the flow of materials and information through your production process, identifying opportunities to enhance efficiency and reduce lead times.
DMAIC Framework: Our team follows the DMAIC (Define, Measure, Analyze, Improve, Control) approach to problem-solving, ensuring that all improvements are data-driven and sustainable.
Define: Identifying key areas for improvement and establishing project goals.
Measure: Collecting data to understand the current performance of processes.
Analyze: Using statistical tools to identify root causes of inefficiencies.
Improve: Implementing solutions to eliminate waste, reduce variability, and optimize performance.
Control: Putting in place control mechanisms to sustain the improvements over the long term.
Kaizen Events: We facilitate Kaizen events (virtual or face-to-face) to drive rapid, incremental improvements in targeted areas. These collaborative workshops bring together cross-functional teams to quickly identify and implement solutions.
3. Waste Reduction & Process Improvement:
One of the key goals of any Lean transformation is to eliminate waste (or “Muda”) in all its forms:
Seven Wastes: We help you identify and reduce the seven forms of waste (Overproduction, Waiting, Transport, Extra Processing, Inventory, Motion, and Defects) within your processes.
Cycle Time Reduction: By streamlining workflows, reducing non-value-added activities, and implementing Lean techniques, we work with your team to reduce cycle times and increase throughput.
4. Enhancing Quality & Reducing Defects:
Our Lean Six Sigma approach also emphasizes quality control:
Root Cause Analysis: We use tools like Fishbone Diagrams and 5 Whys to identify the root causes of defects and quality issues.
Statistical Process Control (SPC): Implementing SPC ensures that processes remain stable and defects are reduced over time, driving continuous improvement in product quality.
Six Sigma Tools: Advanced Six Sigma tools like Control Charts, Process Capability Analysis, and Design of Experiments (DOE) help reduce variability and improve overall quality performance.
5. Change Management & Employee Engagement:
A successful Lean transformation requires more than just tools—it requires a cultural shift within your organization. Our team helps you implement change management strategies to ensure the long-term success of your transformation:
Employee Training: We train employees at all levels to understand Lean principles and equip them with the tools to identify and eliminate waste in their daily activities.
Leadership Coaching: We work closely with your leadership team to ensure they have the skills and mindset needed to sustain a culture of continuous improvement.
Engagement & Empowerment: By engaging employees in the Lean process, we help create a sense of ownership and empowerment that fosters long-term success.
6. Monitoring & Sustainability:
After implementing Lean and Six Sigma improvements, we focus on ensuring that these changes are sustainable over the long term:
KPI Monitoring: We help establish key performance indicators (KPIs) to continuously monitor progress and ensure that the improvements made are delivering tangible results.
Sustained Operational Excellence: Our team helps set up continuous improvement teams to monitor ongoing operations and identify new opportunities for further optimization.